so i figured it was about time to get thae stupid traction bar built as i fliiped the springs etc... so i will walk you throuh what i am doing and answer any questions,
first off there are a ton of different kits and designs and ideas floeting around so i went with my go to guy dan at ruffstuff for the parts and stole some designs from the e net.
here is the kit from ruffstuff
very well designed
then i got the steel tube from a local shop.
hacked off the old tinfoil cross member to build a beefier one
first off there are a ton of different kits and designs and ideas floeting around so i went with my go to guy dan at ruffstuff for the parts and stole some designs from the e net.
here is the kit from ruffstuff
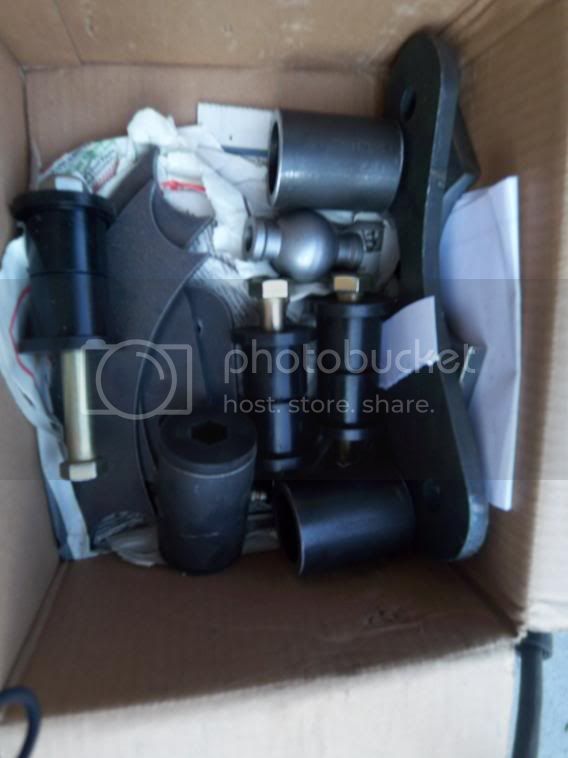
very well designed
then i got the steel tube from a local shop.
hacked off the old tinfoil cross member to build a beefier one
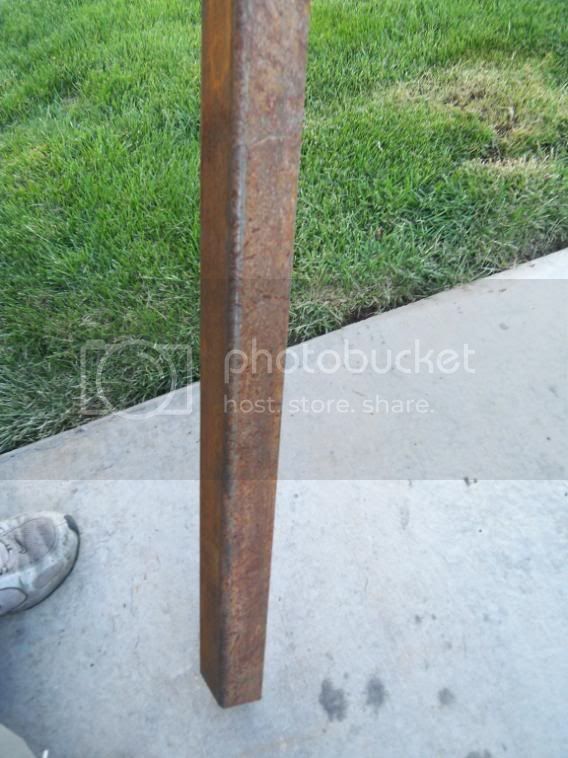