I've had the winch on for a couple of months now and everything seems fine though I've only pulled a few stumps at home and haven't really had the opportunity to give this thing a good work out. I'd like to see what sort of heat is generated in the winch motor and if there are any issues at higher loads but that will have to wait for the moment. Anyway, here's what it looks like fitted up.

The winch sits in nicely though there wasn't enough room to have the spotties and the winch mounted centrally. Options were to 1) space the winch further back into the grill to allow spotties to sit in front of the winch and be central 2) offset the winch and fairlead slightly to the drivers side or 3) offset the spotties slightly to the passenger side. I took option 3) and moved the spotties a little to the passenger side, just off-centre. In hindsight I think perhaps it might've been better to offset the winch a little to the drivers side instead, there's only about an inch or so in it, and having the fairlead off-centre compared with two big spotties probably wouldn't be quite so obvious.

The grill neatly cut and trimmed to fit the larger XP motor. As you can see it only just breaks the profile of the grill.

I wanted to re-use the old 8274 cable remote but didn't know where to mount the socket. In the end I made a bracket between the spotties and I found that that works quite well. And doesn't look too bad either.

I have the in-cab switches located just under the ignition. I got the idea from having seen a few other 100's with switches in the same place, so being short of space for switches I thought this would be a good spot. Unfortunately I've come to realise that the location is not so good for me because I find it really hard to see which switch is which, being on an angle and down so low. And being bit of a tall bloke it's very easy to accidentally knock the switches with my knees. I've only had this for a couple of months and already it's annoying me!
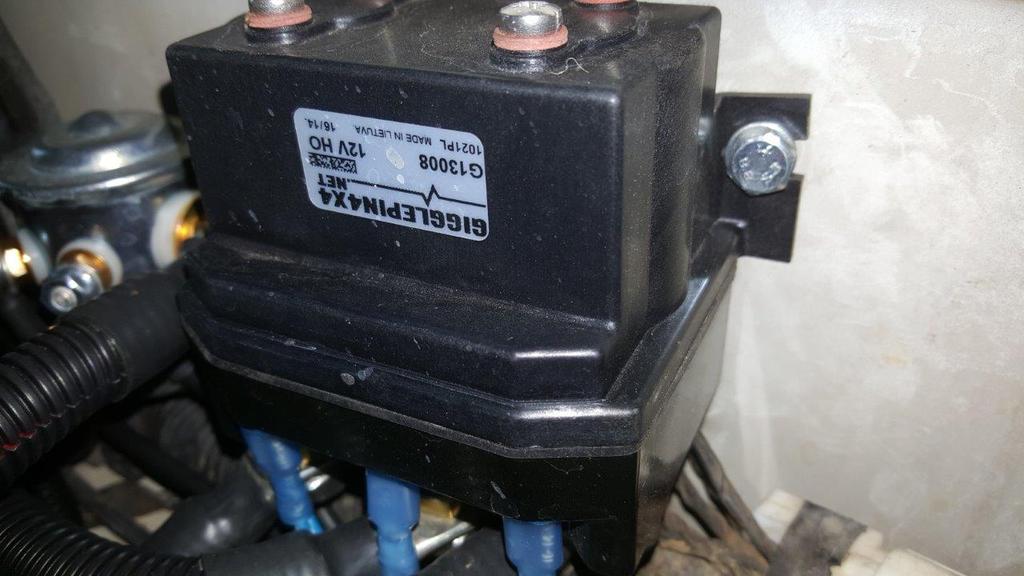
This is the Allbright solenoid pack that I mounted in the engine bay (sits between the airbox and the master cylinder). I know it's a lot easier to mount the solenoids on the winch or on the front winch bar somewhere but I really think in the engine bay will give you much better longevity regardless of which brand you prefer. I got this one from Smithi Engineering (Australian Gigglepin distributor).

At the moment Winch Power is isolated by a 200A Cole Hersee solenoid via the in-cab switch. It's good for 200A continuous load but I'm not sure it's up to the ~480A peak load that Warn says the 8274 will draw at full power. Blue Sea have some good products and I'm looking to find something that might be more suitable....

I fitted a M2K 390XP alternator to the LS3 and according to the specs it will push 220A of charging current at idle. I'm a little concerned about the high amperage going through the hookup. I measured a 1.7V voltage drop when spooling the cable onto the drum so at higher loads I suspect there are going to be some problems. So I'm looking at simplifying and strengthening the electrical system. As I mentioned before I'm no electrical guru so luckily my father has excellent marine electrical knowledge and he's offered to help out here. I probably should've got him involved from the beginning

Specifications from for the OEM 4.6HP motor on Warn 8274-50.