bjowett
Supporting Vendor
Toyota supplies good recovery points on their vehicles, and the 200 is no exception. However, when it comes to certain things, like recovery equipment, bigger and stronger = safer. The Tundra has hooks up front that, IMO, are worth upgrading to. The main hook hoop is manufactured from 1" bar stock, up from .71" on the Cruiser, and the tie down loop is welded in place which provides some cross brace structure. The only down side to these is that they hang about 1" lower. The picture below tells the story. Part number is 51960-0C011, unfortunately, purchase price from Toyota is over $200 for a pair at a good discount. Salavge yards might have them cheap. If you want some delivered, I have several sets of new take off units in stock for $75 a pair + shipping.
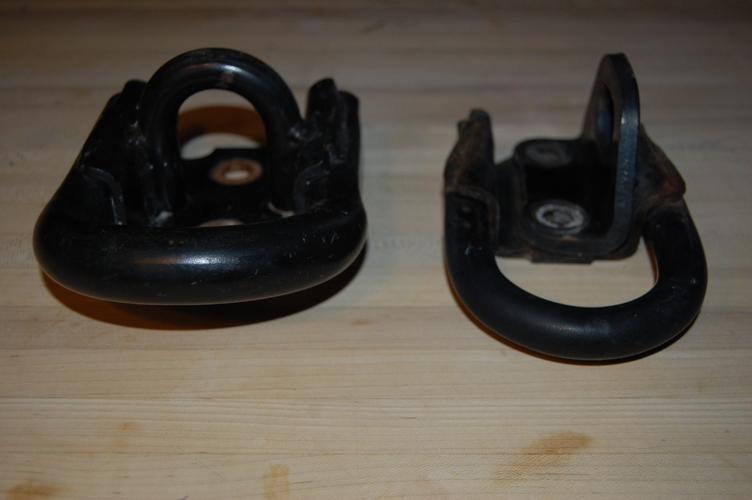
Last edited: