Hornd
SILVER Star
Here are my observations since others may benefit:
Spray all bolts/nuts days before starting with PB Blaster, don't be afraid to repeat.
Hit top nuts with propane torch and quick shot of PB blaster before torquing them loose. Do this several times increasing torch time each time. If they do not loosen, do not snap them off! Instead cut the shock piston shaft with angle grinder and cutting wheel or sawzall.
If you do get bolts out of top or bottom, run a die on the threads. Top bolts are M10x1.25 (Common) and Bottom Sleeve is M12x1.25 Tap (hard to find), Bottom bolt is M12x1.25 (hard to find). Turn the tap with a gear wrench as it is tight swing (see pic). I heated the crap out of the bottom shock bolt before torquing it and it helped a ton, I could not budge them before heat. Be patient.
I found a Metric Heavy Duty washer that will work in place of the bushing washers (see pics) and they cost $1.60 instead of waiting and paying for the OEM washers. They serve a simple purpose (squish bushing) and are Grade 8, so deviating from OEM should not cause Mr T to show up at your door.
Use a brass rifle brush to clean debris out of bolt holes.
Tightened the bushings till they slightly bulged and 3 threads were visible above nut.
Don't put bracket on upside down (Flat side must fit against truck, slotted hole faces wheel). Bracket is upside down in my pic.
It was very satisfying doing this job, but dirty and time consuming.
Drive on ramps make getting under truck easier, but you will still be working on your back. I use a junk fleece coat for dirty work. Lay a piece of cardboard down, to make sliding underneath easier and mess cleanup quick.
Spray all bolts/nuts days before starting with PB Blaster, don't be afraid to repeat.
Hit top nuts with propane torch and quick shot of PB blaster before torquing them loose. Do this several times increasing torch time each time. If they do not loosen, do not snap them off! Instead cut the shock piston shaft with angle grinder and cutting wheel or sawzall.
If you do get bolts out of top or bottom, run a die on the threads. Top bolts are M10x1.25 (Common) and Bottom Sleeve is M12x1.25 Tap (hard to find), Bottom bolt is M12x1.25 (hard to find). Turn the tap with a gear wrench as it is tight swing (see pic). I heated the crap out of the bottom shock bolt before torquing it and it helped a ton, I could not budge them before heat. Be patient.
I found a Metric Heavy Duty washer that will work in place of the bushing washers (see pics) and they cost $1.60 instead of waiting and paying for the OEM washers. They serve a simple purpose (squish bushing) and are Grade 8, so deviating from OEM should not cause Mr T to show up at your door.
Use a brass rifle brush to clean debris out of bolt holes.
Tightened the bushings till they slightly bulged and 3 threads were visible above nut.
Don't put bracket on upside down (Flat side must fit against truck, slotted hole faces wheel). Bracket is upside down in my pic.
It was very satisfying doing this job, but dirty and time consuming.
Drive on ramps make getting under truck easier, but you will still be working on your back. I use a junk fleece coat for dirty work. Lay a piece of cardboard down, to make sliding underneath easier and mess cleanup quick.


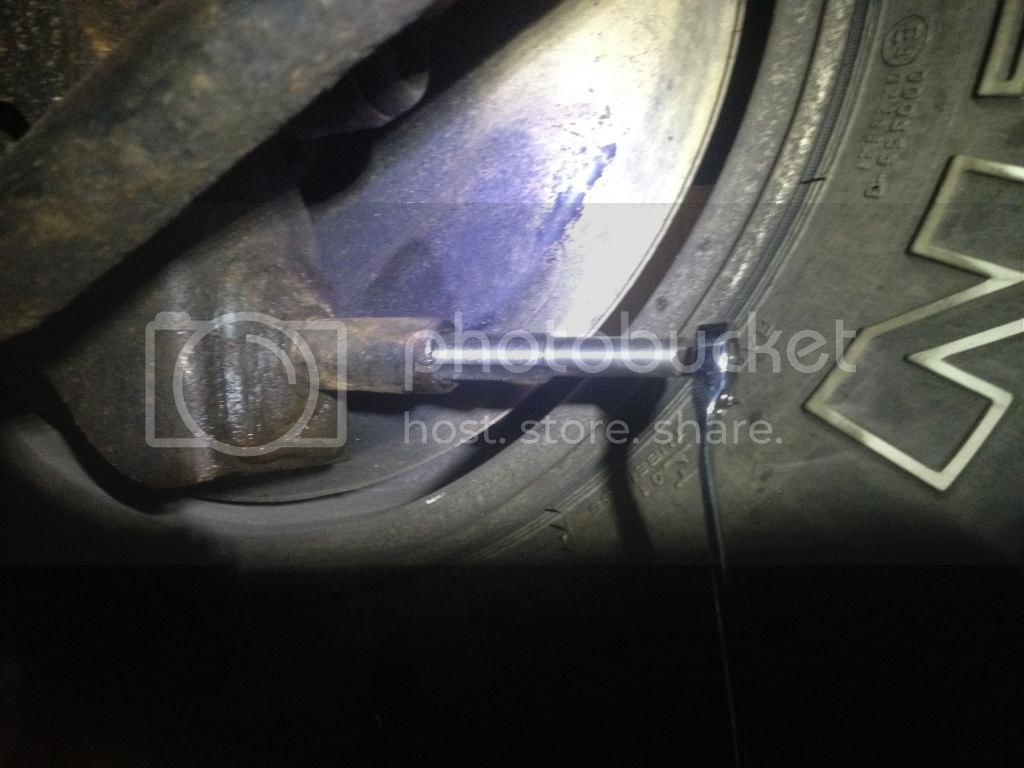



Last edited: