Started building a welding table for my garage finally! Used the upper dimensions of 5'x3' for the table top and then set the frame in 4" from the edges of the table. Legs are 3' tall, then the runners are 4' long and 2' long respectively. Bottom runners are elevated 6" from the bottom of the legs. Had the majority of the cuts done by the steel yard I picked up the 2x2x1/8" wall tube from.
I'm posting this thread up because I need ideas for "essentials" of any good welding table. I'm thinking hooks for my grinders, maybe a mounted power strip for them as well, slots in the middle for clamping purposes and finally mounting a good vice on one corner. To make it mobile, I want to do something like the Home Depot rolling staircases, where you have a foot activated lever to extend the casters down, and then after pressing the lever again, the staircase drops down and rests on the floor. I still need to come up with that design.
I'm hoping y'all have some good ideas for me!
Here's what I've done thus far (top is not welded to the frame, nor is the frame fully welded at this point):
I'm posting this thread up because I need ideas for "essentials" of any good welding table. I'm thinking hooks for my grinders, maybe a mounted power strip for them as well, slots in the middle for clamping purposes and finally mounting a good vice on one corner. To make it mobile, I want to do something like the Home Depot rolling staircases, where you have a foot activated lever to extend the casters down, and then after pressing the lever again, the staircase drops down and rests on the floor. I still need to come up with that design.
I'm hoping y'all have some good ideas for me!
Here's what I've done thus far (top is not welded to the frame, nor is the frame fully welded at this point):


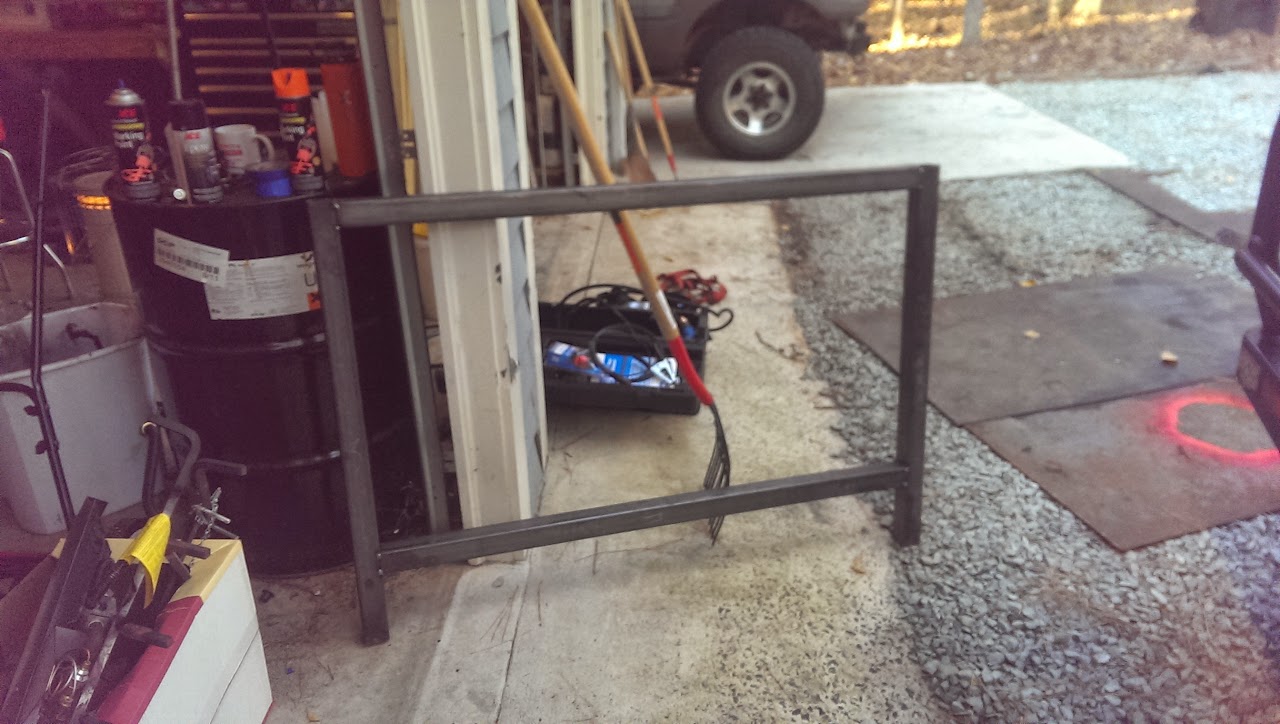


